Camless diesel engine since 1999
Can you imagine your
diesel engine idling on 3 cylinders or having 3 compression strokes to
one exhaust stroke? How about an engine brake like the big boys instead
of a exhaust brake on your pickup diesel? Or having your left cheek
vibrating along with a buzzer when you cross the yellow line heading
toward ongoing traffic. There are important innovations very close to
reality as truck options, that even the late Gene Roddenberry of Star
Trek fame, couldn't have dreamed up. From camless engines that can on
demand switch from a 4-stroke to a 2-stoke to even a 8-stroke, to gyro's
similar to what cruise missiles use, telling computers to control the
speed and brakes on your trucks, even steering with the truck's brakes.
It's exciting and even hard to imagine. This new technology can make it
possible for diesels to lead the way for clean air, similar to the
direction Europe is heading verses the hydrogen cell solution that is
getting the press and political support in this country. Another leading
edge technology, is the camless engine. Camless engines are alive and
well, with Bosch, announcing their entry into the camless race earlier
in 2003.
Sturman Industries
started developing the camless diesel engine in 1995 as a natural
progression from their electro-magnetic digital valve actuator already
developed for fuel injectors for International in 1993. Sturman
Industries founded by Eddie Sturman, using technology he developed for
the retro rockets of the Apollo spacecraft, uses residual magnetism in a
digital valve to open and close valves or control the hydraulic pressure
activating fuel injectors. The 6.0L Ford Power Stroke diesel introduced
in 03 uses the Sturman Industries digital valve in the SDST injectors
manufactured by a joint Venture of Navistar/Siemens AG
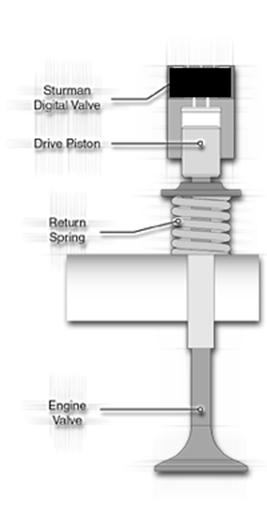 |
Sturman DHOS™ Valve Actuation Module
The high power to mass ratio of electrohydraulic actuators
facilitates the development of camless engines where timing the lift
and closing of the intake and exhaust valves for different engine
speed and load conditions has the potential to improve efficiency
and torque and reduce emissions.
In
its simplest form the
design of the DHOS™ Valve Actuation Module consists of an
electrohydraulic actuator (featuring a
Sturman Digital Valve) acting upon a spring returned engine
valve. The replacement of the mechanical valvetrain with a fully
variable camless actuation system provides the
operational flexibility required to control mass transfer of
intake air and exhaust into and out of the engine cylinders.
The
return spring on the valve acts as a failsafe to insure the valve
would close incase of hydraulic failure and not damage the engine.
Picture courtesy of Sturman™
Industries
|
Near the middle of
a mountain range near Woodland Park Colorado, with a view of Pikes Peak
(14,110 ft.) shared by the engineers on all 4 floors at Sturman
Industries, magic happens. This facility that looks more like a Ski
Lodge than the international R&D center it is, to inspire the creativity
needed to develop the ideas from Eddie Sturman and his motivated
engineers. In an interview with Carol Sturman, president of Sturman
Industries, I learned of some of the possibilities with Sturman digital
valves. The dramatic difference between analog and digital, relates to
electrohydraulic actuators as well as cell phones and PC's. Co-founders
Carol and Eddie Sturman lead their company with a philosophy of
improving the earth by creating a efficient clean burning engine.
Imagine again first to rid the engine of camshafts, rocker arms,
pushrods, lifters, bearings, timing gears, etc. And as you Dodge diesel
folks know, your inline 6-cylinder engine has 30% less parts than a V-8
diesel, now it's possible to have even less parts to wear and drag on
engine power and fuel economy. With a lighter, faster, more fuel
efficient and cleaner burning engine in diesel or gas.
Using a digital
valve to control how much, how often, and how fast each individual
engine intake and exhaust valve moves, is were it starts. This control
is why the camless engine would have free quieter engine braking
capability with engine braking each stroke and quicker engine warm-up.
Yes engine braking like the big boys. Even having 3 compression strokes
before an exhaust stroke to use up all the fuel and less need for after
treated exhaust. Sturman's digital valves would enable you to change the
valve settings, seating velocity and duration etc. like having a 3/4 RV
cam, full race cam or anywhere in-between, providing lower end towing
torque and a cooler running engine with less NOx emissions. With so many
variations possible with the digital valve controlling better engine
breathing at all rpm's, individual variable cylinder compression
ratio's, you could even shut the engine down to just 3 cylinders when
idling for noise reduction and less fuel consumption. Just shutting off
a diesel would be quicker without the shudder by digitally controlling
the valves to all close.
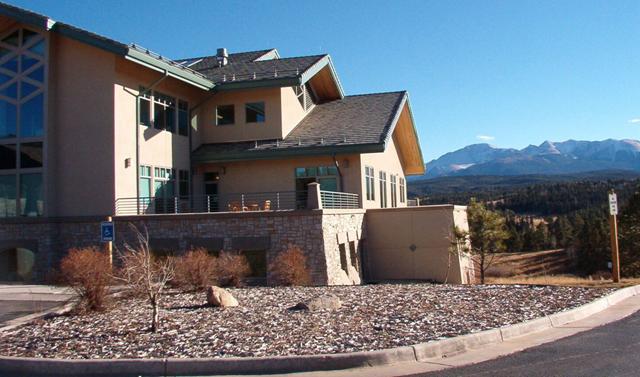
|
Sturman Industries
World Headquarters, looks like a ski lodge just north of Pikes Peak
nestled in the Colorado Rockies. Working there couldn't be called
work, I saw the fireplaces, pool table and sun decks. Even ports for
your laptop on the south deck. Eddie and Carol Sturman wanted their
people to all share in the view with large windows on the south
side. I felt like John Denver just visiting. It makes sense to have
your company located in the middle of nature when your company
philosophy is improve the environment. |
I've been invited
back to the mountain at Sturman's to drive one of their two famous
Navistar medium duty trucks that have already toured 10,000 miles of the
country with camless diesel engines. In 2000 Sturman Industries
sponsored the famous Pikes Peak International Hill Climb after already
climbing the mountain to it's 14,110 ft. peak with their camless diesel
truck. Where else would you test a diesel truck? I'll report back after
my test drive when I'm "back to the future."
David Burt, Sturman
engineer, gave me a tour of the R&D facility near Woodland Park,
Colorado. We looked over rows of sophisticated testing equipment, with
dyno testing cells. In high altitude, they have to do some work to
stimulate sea level. It's an advantage testing diesels at high
altitudes. According to Burt, Sturman Industries are working close with
the EPA and Department of Energy in developing a clean burning diesel.
Which I'm glad to see progress in diesel as an alternative fuel for the
future with government evolvement. Sturman's commitment to safety is one
of the reasons their products are low pressure common rail with the high
fuel pressure intensifying inside the injector.
With Sturman
digital valve injectors in development in 1993, and production in 2002,
don't be surprised to see the Sturman digital camless engine out before
the Tier 2 emissions go into effect in 2007. Then next it looks like the
Sturman's Combustion Cell with integrated digital fuel injection and
valve actuation together in individual cylinder unit's.
Gas engines can
have their own advantages using the digital valve. Sturman's test engine
has run at 15,000 rpm's. A gas engines throttle plate would be
eliminating using the variable valve lift to control air flow. 16% fuel
mileage improvement has occurred on gas engine testing. And the much
talked about cylinder deactivation is possible with the Sturman Digital
valve. Of course again, it works with gas engines too, when you can
control valve timing and air flow you get more low-end torque.
Sturman's have
tested a VW Jetta with their digital injectors. They are working with VW
on using renewable fuel from Biomass. Imagine growing fuel, using it and
the exhaust from your engine feeds the growing fuel. Sound like Lion
King's the "Circle of Life."
Sturman Industries
are building products for 8 major engine OEM's as well as the EPA and
Department of Energy. So we shall see who brings the camless diesel to a
pickup truck first and second and etc.
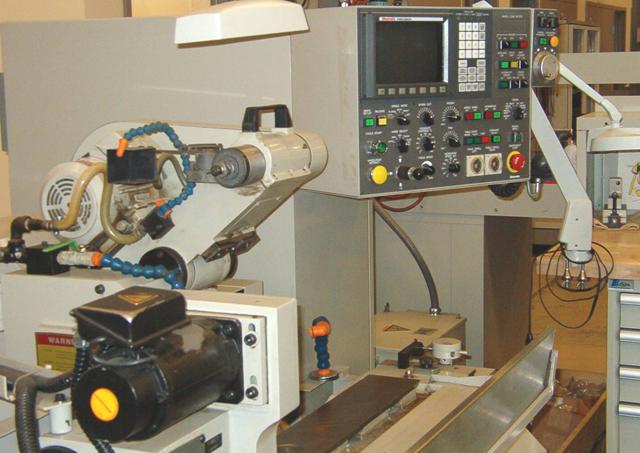
|
My tour included rows and rows of
testing machinery for high pressure hydraulics. Looked like NASA.
Sturman's make all the components they use in prototype testing. A
lot of brain power there! |
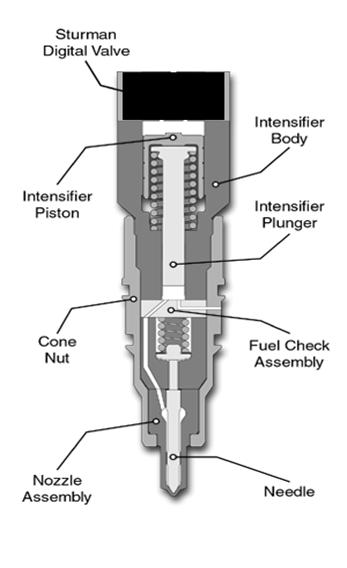
|
Sturman DHOS™ Injector
The application of electrohydraulic actuators in fuel injectors
provides the ability to control the rate of injection such that fuel
economy is improved and emissions of hydrocarbons and NOx can be
reduced.
The incorporation of the Sturman Digital Valve into the design of
the injector provides operational flexibility in the control of main
and pilot fuel quantity, timing, and duration.
The Sturman DHOS™ injector has the capability of electronically
controlling the rate of injection (ROI) characteristics needed to
meet future engine, emissions, noise, and drivability requirements.
The
6.0L Ford Power Stroke diesel introduced in 03 uses the Sturman
Industries digital valve in the SDST injectors manufactured by a
joint Venture of Navistar/Siemens AG
The
digital valve is the trigger, hydraulics are the driving force in
the high pressure injector from a low pressure common rail system.
Picture courtesy of Sturman™
Industries |
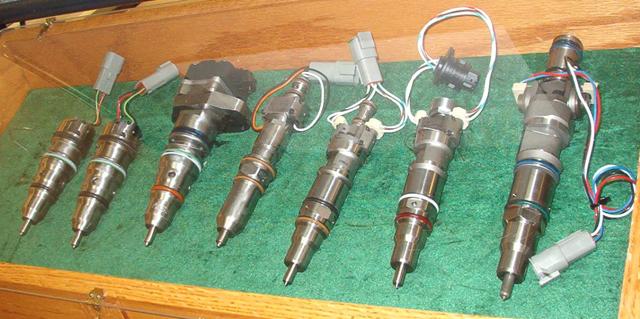
|
From the original
Hydraulic Electronic Unit Injection (HEUI) diesel injector (above
third from left) developed by Caterpillar and International to the
smaller more efficient electrohydraulic Sturman prototypes (above
next to HEUI with smaller barrels) from Sturman Industries licensed
to Siemens Diesel Systems Technology for production in
Navistar/International diesels including the 6.0L Ford Power Stroke.
The SDST G-2 smaller Sturman valve actuated fuel injector, built in
Columbia SC, allowed Ford/Navistar to go from 2 valves per cylinder
to 4 valves in the 03 6.0L Power Stroke diesel. The fuel injection
system in Navistar diesels uses low pressure common rail (3000 psi)
in the heads where the high pressure is built up in the injector
verses Duramax and common rail Cummins using high pressure external
common rail being forced into the injector. |
The 03 Ford Power
Stroke, has had it's share of problems. So for 04 Ford, is moving the
Injection Control Pressure sensor to the front of the engine, using
longer glow plugs, and an anti-foam Stanadyne additive to prevent
foaming in a diesel engine with the largest oil capacity of the big
three. The Ford Navistar diesel hold 15 quarts including the filter.
Part of this oil capacity functions as the hydraulics for the low
pressure common rail fuel injection and actuating the new in 03 variable
turbo called EVRT. Also Ford has discontinued using the pilot injection
introduced in the 03 Power Stroke 6.0L model according to Roger Judson
Product Design Engineer for Ford. Pilot injection was introduced in the
03 Power Stroke to lower noise and reduce NOx emissions. GM's Duramax
lead the way in 01 with pilot injection, with the Dodge common rail
Cummins pilot injection also introduced in the 03 model.
for
more visit
www.sturmanindustries.com
Lane Departure
Warning System
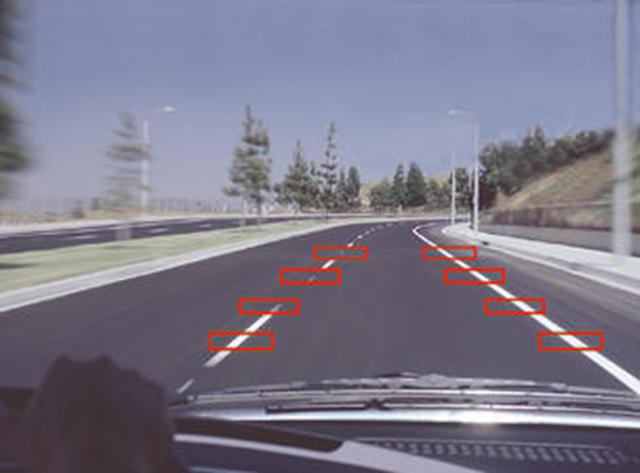
"Martha my butt's vibrating!" Calm down Henry, it's just the new lane
departure accessory I bought you for Christmas to keep you from
falling asleep at the wheel again." The lane departure warning system
called Autovue™ by Iteris is on hundreds of semi-trucks now across the
country, testing the effectiveness of left and right non intentional
lane change warning. Where I live in Colorado we have snowplows. So the
lane bumps you see in states like California and Nevada aren't possible,
for long anyway.
Iteris is the company that manufactures management systems, sensors and
camera's for traffic light intersection management. No not all those
camera's are taking your picture for running a red light or speeding.
Iteris camera's monitor traffic and the computer system manage which
lanes have the most traffic and need a longer signal.
This same technology
tracks lane markings to give you "Lane Departure Warning." Your turn
signal deactivates it when you want to change lanes without the warning.
There are warning lights, left and right speaker, and on deluxe models
offered on semi trucks, a left and right seat vibrator. That would
explain some smiling truck drivers.
AUTOVUE™ LANE
DEPARTURE WARNING (LDW) SYSTEM
Unintended lane
departures are the single largest cause of
fatalities on
U.S. highways. Over 43 percent of all fatal accidents in 2001 reported
lane or road departures as a contributing factor. (Source: NHTSA FARS
database.) Rumble strips on the outside of the road have been proven to
reduce lane departure accidents by 30-55 percent. But we all can't have
those bumps. Iteris’ LDW System is a small, integrated unit consisting
of a camera, onboard computer and software that attaches to the
windshield, dashboard or overhead.
Iteris’ LDW System is
programmed to recognize the difference between the road and lane
markings. The unit's camera tracks visible lane markings and continually
feeds the information directly into the unit's computer, which combines
this data with the vehicle's speed. Using image recognition software and
Iteris proprietary algorithms, the computer can detect when a vehicle
begins to drift toward an unintended lane change. When this occurs, the
unit automatically emits the commonly known rumble strip sound, alerting
the driver to make a correction. When activated, Iteris’ LDW System
works effectively both day and night and where lane markings are
visible.
I drove a Ford F150
with this system in Denver. It picked up the perimeters of the lanes
well even in area's of construction where there where new lines on top
of old lines.
Additional features
include:
·
An Active
Headlamp Control algorithm that senses ambient light and
automatically turns the headlamps on or off. An enhancement to this
feature resides in its ability to sense tunnels approaching and activate
the headlamps at the beginning of the tunnel.
·
A Rain
Sensing feature that can be used to turn windshield wipers on and
control their speed. I wonder if they vibrate.
·
A Blind Spot
Warning feature that monitors the adjacent lanes of the vehicle. If
the driver signals his intention to change lanes, an audible warning is
generated if there is a vehicle already occupying that space. I could
use this in Denver.
Iteris first announced
their AutoVue™
Lane Departure Warning System in 1999. In 2000 DaimlerChrysler Venture
GmbH invested in Iteris to adopt the in-vehicle sensor in
DaimlerChrysler commercial vehicles and passenger cars. That same year
Mercedes adds it as an option to the new Actros trucks in Europe.
Freightliner offers the Iteris "Lane Guidance" as an option in 2002 on
Century and Argosy trucks.
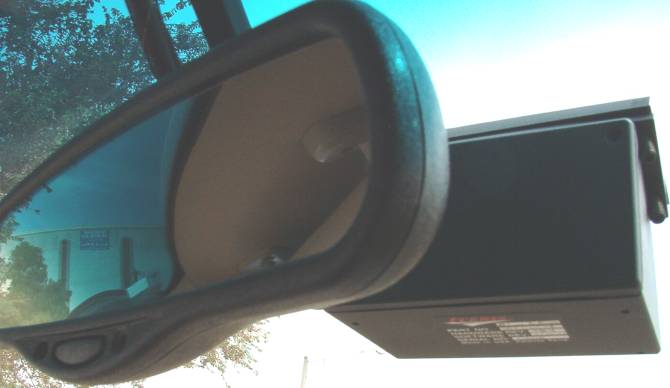
|
The Autovue™
camera that tracks all visible lane markings mounted behind the
rearview mirror. This prototype box is refined and smaller in the
Mercedes Benz car of course. |
Electronic Stability Control,
understanding Vehicle Dynamics
Now
here is were the cruise missile gyro's mentioned at the beginning of my
article, come into the story. Skidding out of control on slick roads,
curves or the moose in the road, is the purpose of Continental
Automotive Systems, Electronic Stability Control (ESC.) With 700
rollovers a day in this country, the subject is important and the
solution is now available on many vehicles. As usual, trucks are on the
bottom of the technology option list with luxury cars at the top. The
2004 Nissan Titan truck I reviewed had Electronic Stability Control.
It's an option on all major SUV's now and standard on most European
luxury cars.
But
trucks could benefit the most being nose heavy empty and rear heavy
loaded. If you've experienced driving a 4x2 truck without a load on
slick roads, you know what I'm talking about. Even a 4x4 truck with no
weight in the bed can be squirrelly when the weather turns ugly.
Anti-Spin or limited slip differentials can help in those situations.
Cars have the option of traction control, which is just ABS brakes being
applied to the spinning wheel so the opposite wheel has traction, like
turning brakes on a farm tractor. ABS (anti-lock brake system) and TSC
(traction control system) are a big part of ESC.
ESC
with it's microcomputers starts the process of giving you back control
of your vehicle, when the sensors detect a problem before you do. The
sensors, wheel speed sensors, steering wheel angle sensor (steering
wheel angle and input rate), yaw sensor (the gyro, vehicles rotation
around it's vertical axis), and lateral acceleration sensor,
(acceleration of the vehicles vertical axis, side to side motion). All
this in milliseconds, actually 140 signals to the ECU (control computer)
a second where the appropriate action is calculated and implemented in
less than a second. Faster than me on a good day.
Basically there are three components to Electronic Stability Control.
The Gyro which is located near the vehicles center of gravity next to
the Yaw axis. The Gyro detects motion whether, it's the trucks pitch or
roll and tells the computer what's happening and the steering sensor
tells the computer if you are steering in a different direction than
your truck is heading. The second component of a ESC is decelerating the
engine and then the computer tells each brake through the ABS system
with traction control, which of the four or combination of brakes, how
to steer the vehicle in the direction you intended it. This is an over
simplification of the process but in real life if works seamlessly and
very fast.
The
system automatically detects impending wheel lock up, wheel spin or loss
of vehicle control. Then regulates speed, and applies brakes where need
to control the vehicle when you can't. Continental partnered with
Volvo, to give us a first hand experience driving Volvo XC90 SUV with
ESC. Our test track was an empty parking lot big enough to land 737's at
Coors Field baseball park. A water truck assisted in giving us a slick
surface. A couple of courses were set up with cones simulating a quick
lane change and a sharp curve, on ramp. On the quick lane change on
slick asphalt, the Volvo handed great, no loss of traction or skidding.
On the sharp curve I held my line and didn't get pushed to the outside,
the ESC corrects the oversteer and fish tailing you normally get by
applying the outside front brake. I love these test drives, it's not my
car!
I know
it seems strange steering with brakes on slick conditions, because we
are use on not using brakes in bad conditions. But when a computer can
manage all the data coming in from sensors in a second or two, using the
pulsating ABS brakes to brake just a little and not lock up, it does
work. But because of the complexity of it, education is the key to
spreading the word that ESC can and does save lives. To see what it's
like with and without it on the same vehicle driving the same course,
makes me a believer as we were able to shut ours off in the Volvo XC90
SUV test vehicles. The majority of SUV's now have their branded names of
ESC available as an option. Nissan Titan is the only full size truck
with the option in 2004. Hopefully it will soon be an option on pickup
trucks.
By the
way Continental Teves makes the majority of ESC systems, each
manufacture likes to create it's own name, like Electronic Stability
Program for DaimlerChrysler, GM StabiliTrack, Ford AdvanceTrac, Nissan
Vehicle Dynamic Control, and Toyota calls theirs Vehicle Stability
Control. The Society of Automotive Engineers, (SAE) will soon make the
official term ESC so we can talk about the same thing as with ABS and
SRS.
In
situations where you would need and use ESC, it would happen faster than
you could react, which is part of the benefit. In an understeer and
oversteer situation ESC would use pulsing individual brakes to help
steer in your intended direction. Say if you were skidding to the right
in a snow storm while you where steering to the left, in milliseconds
the ESC system knows the vehicle is traveling to the right because of
the steering sensor and the gyro in the yaw stability system tells the
computer you are skidding. So the front right brake is pulsated to steer
left and and the same time the ESC computer slows the engine down.
On
another day of testing Volvo XC90's with Volvo, I was taught their
"Moose Maneuver". Must be moose in Sweden, though my grandparents didn't
mention it. But it does sound like a good idea to avoid hitting the
moose in the middle of the road. Here in Colorado we have a similar
experience with Elk. An animal that big could probably do more damage
coming threw your windshield and setting next to you than rolling your
vehicle down the ditch unless the ditch is a few hundred yards straight
down, then another decision would have to be considered. But anyway,
after a demonstration, on an open stretch of pavement at 40 mph, I
swerved from outside line to opposite outside line and survived. It was
scary and the SUV did lean quite a bit but I never lost control and if
there had been a moose in the road I probably would have missed it. The
Volvo XC90 SUV has ESC and their Roll Stability Control, so besides
controlling the vehicle it also keeps the shiny side up and the greasy
side down. A good thing.
Another advance with ESC is coming from Delphi and will be first seen in
GM trucks using the Quadrasteer. So along with the computer assisting
with ABS to steer the vehicle in the direction you intended,
Four-Wheel-Steer integrated with Traxxar™
will help correct direction by steering the rear wheels. We're getting
closer to driving like the "Jetsons."
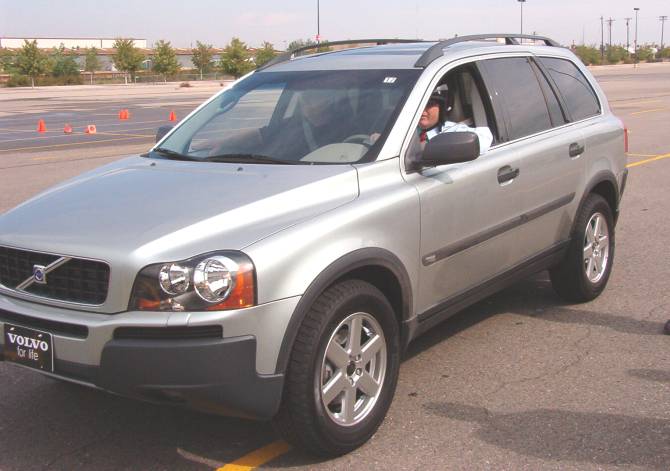
|
Continental had a
water truck pouring water on our course. We needed it, the press can
get carried away in our search for knowledge. The XC90 Volvo is
all-wheel drive and doing evasive maneuvers on dry pavement can get
exciting with too much traction. But water on the asphalt did show
how well Electronic Stability Control works when you need it. Notice
a few knocked over cones in the picture above, that's how you know
we are professional drivers, not. Continental Automotive Systems is
a division of Continental Teves North America. The folks who
pioneered ABS brakes. They make tires too. HOME
PAGE 1
TOP 2
PAGE 3
PAGE 4
Your Online
Pickup
Truck,
SUV &
Trailer
Resource Magazine. |
|
|